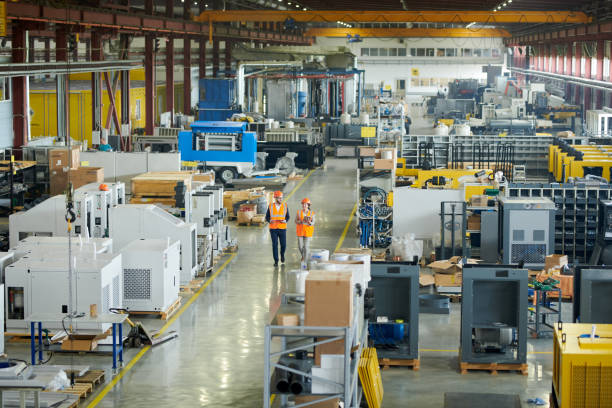
Globalization and technological advancements have made the world evolve in many ways. With the rapid advancement of technology in today’s world, everything is changing, from the way we talk to even the way we think. Humans can’t really function in today’s world without technology because technology has been embedded into our daily lives, from our wallets to everything in our home. Technology also plays a large role in the professional industry. Thanks to technologies’ finest advancements, we now have factory automation system, which we will be talking more about, so keep reading on.
What is a factory automation system, you ask? Well, the use of technology and automation systems in manufacturing processes is what we call factory automation. It has the primary goal of increasing productivity in the industry while also lowering costs of operations. Though, the degree of which the automation occurs ranges from complete human involvement (meaning the system needs to be manned and controlled by a human) to complete automatic operation (no human needed).
Factory automation systems are automating tools that humans use to operate production processes with controllers, computers and other controlling devices. The goal of using these systems is to cut off human or manual intervention during manufacturing processes, to basically cut the cost of hiring people to manually recreate what these machines can now do. It is very important in the industry to reduce material waste, boost output, as well as increase the quality of products all while reducing costs in different areas. It can also create safe working conditions so that humans don’t get involved too much with heavy machinery, as there have been many accidents associated with these dangerous equipment.
There are three different types of factory automation system. Firstly we have single automated factory automation. As the name suggests, single automated factory automation is when a machine automates a single repeated process. This can include inspection, welding, packaging or any ONE action that requires a repeated process. Components can be manually placed and inserted into a machinery, which means it is not suitable for any circumstance where a user needs to add more equipment to execute any other function other than the one single action.
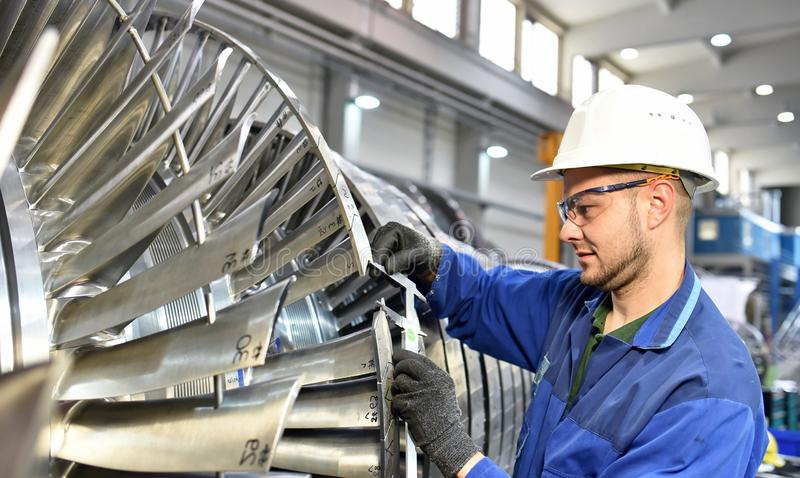
Next, we have automated production lines. This is when a whole collection of machines are connected by a system called the transfer and electrical control system. With automated production lines, there will be a specific product to be processed in a sequence. It will pass along a line of pre-determined production steps with various different work stations performing a particular step of the production process, like colouring, indent, marking or even labelling. The sequence will be laid out and whether or not you need a human to man the station is determined by how much the automation is being utilized. Usually with this type of automation, operators will be required to supervise and monitor the machinery.
Fully automated is the last type of automation we know. A fully automated factory, exactly like what the name suggests, will not require a worker or operator to supervise. It can complete all functions on its own, and it can also self-adjust, as well as complete product quality measurement on its own.